Comprehensive Guide to Industrial Plastic Molding and Plastic Injection Molding Techniques
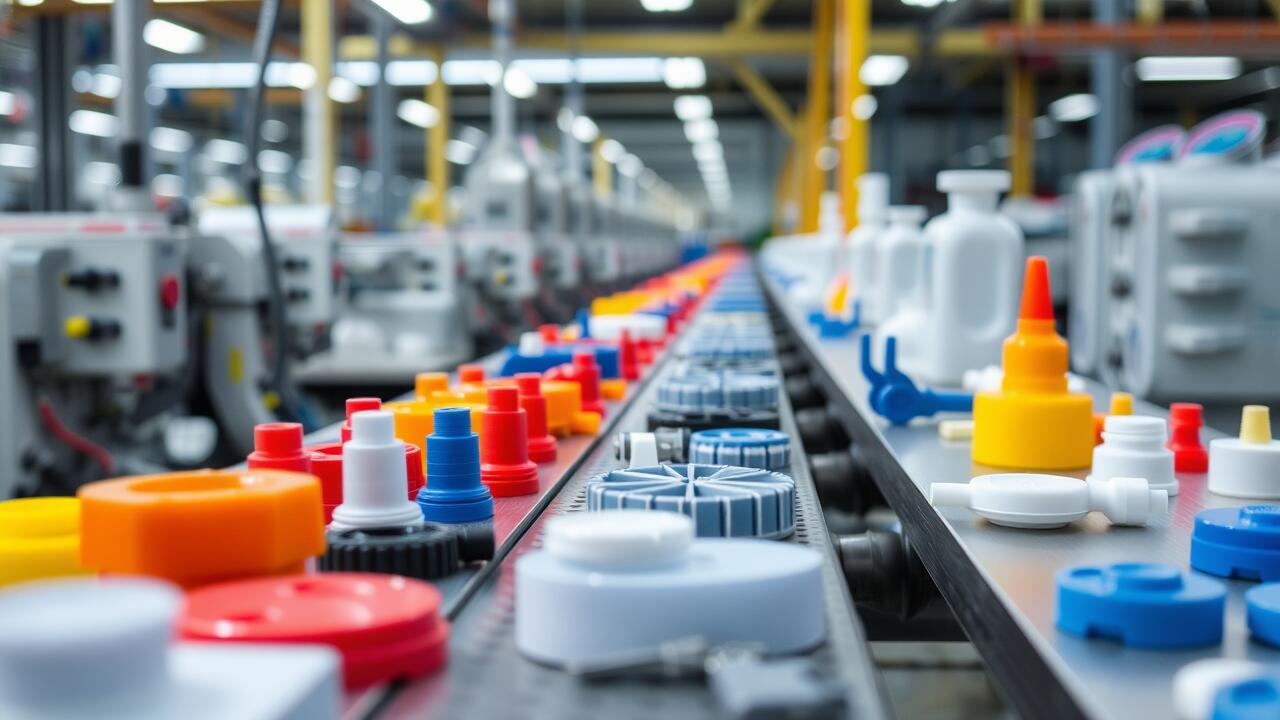
Table Of Contents
Overview of Industrial Plastic Molding
Industrial Plastic Molding refers to the process of creating plastic parts and products using various techniques, particularly plastic injection molding. This method involves the use of an injection molding machine to melt plastic and inject it into a mold, forming the desired shape as it cools. The efficiency of plastic injection moldings allows for rapid production of intricate designs and detailed components. Molds play a crucial role in this process, as they dictate the final shape and quality of the finished product. With advancements in technology, modern injection molding machines have become capable of producing high volumes of consistent and precise moldings, making Industrial Plastic Molding a cornerstone in various manufacturing sectors.
Definition of Plastic Molding
Industrial plastic molding refers to a manufacturing process that shapes plastics into desired forms using specialized molds. The primary methods include injection molding, blow molding, and extrusion molding. Each technique utilizes different types of molds, such as injection molds for creating intricate parts and blow molds for hollow objects. These processes allow for efficient production of plastic components in various industries, from automotive to consumer goods.
The versatility of plastics makes industrial plastic molding a critical aspect of modern manufacturing. Injection molding is optimal for producing complex geometries, while blow molding is ideal for creating lightweight containers. Extrusion molding allows for continuous shapes such as pipes and sheets. Understanding these molding techniques is essential for engineers and manufacturers to achieve high-quality results tailored to specific applications.
Importance in Manufacturing
Industrial Plastic Molding plays a crucial role in modern manufacturing processes. Techniques such as injection molded, compression molding, and rotational molding allow manufacturers to create intricate shapes and designs with high efficiency. The versatility of molten plastic enables the production of a wide range of products, from everyday plastic bottles to complex automotive components. This adaptability makes Industrial Plastic Molding indispensable across various sectors.
The significance of moulding in manufacturing is not just about efficiency but also about cost-effectiveness. Processes like extrusion moulding promote mass production while maintaining quality standards. With the ability to reproduce parts consistently, manufacturers can rely on the precision of molded components to meet their production needs. This reliability enhances product performance and drives innovation in multiple industries, reinforcing the value of Industrial Plastic Molding.
Types of Plastic Molding Processes
Industrial Plastic Molding encompasses a variety of processes that shape plastic materials into specific forms using moulds. Injection moulding is a prevalent technique where melted resin is injected into a mould, allowing for high precision and rapid production. In contrast, blow moulding is used to create hollow parts, often found in bottles and containers, by expanding hot plastic within the mould. Another method, rotational moulding, involves rotating a heated mould filled with resin, resulting in uniform thickness in products like jello molds. Each process has distinct advantages and applications, making the choice of method critical in achieving the desired quality and efficiency in manufacturing.
Injection Molding
This process is a vital technique in industrial plastic molding, allowing manufacturers to create complex shapes and designs with high precision. It involves melting thermoplastic materials, such as polyethylene, and injecting them into a mold. Tool steel molds are commonly used, as they withstand the high pressures required during this phase. The efficiency of injection molding makes it a preferred choice over other methods like rotomoulding and compression moulding for mass production of plastic parts.
The versatility of this method permits the use of various raw materials, including powders and granules. Adjustments to temperature and pressure settings can be optimized to achieve desired characteristics in the final product. As industrial plastic molding evolves, innovations continue to enhance production speed and quality, making injection molding a cornerstone of modern manufacturing processes.
Blow Molding
This molding technique plays a crucial role in the production of hollow plastic parts, making it essential for various applications in the automotive industry. The process utilizes machines that can handle materials like polyethylene or polypropylene, ensuring that products such as recycling bins and cylinders are efficiently produced. By leveraging extrusion, manufacturers can create lightweight yet durable components, with designs tailored to specific industry needs.
The versatility of blow molding extends beyond conventional materials, as it can incorporate advanced composites like stainless steel and 7075 aluminum for enhanced durability. Industries are increasingly adopting this method due to its efficiency in producing intricately shaped parts while minimizing waste. As a result, many sectors, including the automotive industry, benefit from the high-performance characteristics that blow molding offers through Industrial Plastic Molding techniques.
Extrusion Molding
This process is a vital technique within the realm of industrial plastic molding. It involves forcing melted plastic through a die to create long shapes, ideal for producing items like pipes, sheets, and films. The method is highly valued for its efficiency and ability to work with various polymer materials. Plastic molding specialists frequently use metal molds, which allow for consistent production molds that maintain high standards of quality and precision. Moreover, the technology supports recycling efforts by enabling the reuse of plastics, contributing to environmentally responsible manufacturing practices.
Applications of this molding technique are extensive, providing solutions across numerous industries. From creating components for packaging to producing durable construction materials, the versatility of this method is unmatched. Plastic molding technology continues to evolve, integrating advancements that enhance production capabilities while reducing costs. As manufacturers seek to optimize their operations, the use of industrial plastic molding through extrusion techniques ensures they remain competitive in the market. The ability to mold complex shapes efficiently makes it a preferred choice for many industrial applications.
The Role of Molds in Plastic Molding
Molds serve as a critical component in Industrial Plastic Molding, shaping the plastic material into various forms. These mold tools determine the design and specifications of the final product, whether it involves full production molds or custom plastic parts. High-quality plastic moulds ensure that each cycle produces consistent plastic parts with precision. As the plastic material cools within these molds, the temperature and pressure settings play a pivotal role in achieving the desired outcomes. A complete mold is essential for maximizing efficiency in production, allowing manufacturers to meet the demands of various industries while maintaining high standards in quality and performance.
Types of Molds Used
Molds play a critical role in Industrial Plastic Molding, dictating the quality and precision of the final products. Molding dies are among the most common types used, specifically designed to create solid plastic parts with exceptional accuracy. These dies can accommodate various plastic resins and are tailored for different manufacturing processes. For projects requiring low-volume production, prototype molds are essential, allowing manufacturers to test designs and functionalities before committing to full-scale production.
Another important category of molds includes roto-molding tools, which are designed for rotational molding processes. These tools are predominantly used to produce hollow plastic parts, beneficial for applications like plastic replacement parts. As plastic powder developments continue to evolve, the versatility of molds expands, enabling manufacturers to achieve intricate designs while maintaining cost-effectiveness in Industrial Plastic Molding. The choice of mold significantly influences quality, production speed, and overall efficiency in manufacturing processes.
Custom vs. Standard Molds
Custom molds are tailored to specific design requirements, making them essential for unique applications in Industrial Plastic Molding. These molds are often used for creating hollow plastic products through processes such as modern rotational molding. Heated plastic material is injected or formed into these molds, allowing for detailed and complex shapes that standard molds may not accommodate. A pmt plastics manufacturer often provides custom mold solutions to meet the demands of businesses seeking specialized plastic components.
Standard molds, on the other hand, are pre-designed and used for mass production of common shapes. They facilitate cost efficiency and quicker turnaround times in projects that do not require customization. Melted plastic is poured into these molds, which can include compression molds or thermoform molds, ready for immediate production. For companies focused on high-volume output, standard molds in Industrial Plastic Molding serve as an effective solution for maintaining consistency and quality across large batches.
Applications of Moldings in Various Industries
Industrial Plastic Molding plays a crucial role across various industries due to its versatility and efficiency. The process begins with raw plastic, which is heated into a liquid state or hot plastic, enabling it to fill cavity molds with precision. For instance, in the automotive industry, plastic injection techniques ensure the creation of lightweight components that enhance fuel efficiency. The consumer goods sector benefits from thermoform molds that produce plastic sheets for packaging, while medical devices require high-quality plastic retains that meet stringent safety standards. Each application highlights the importance of Industrial Plastic Molding in manufacturing innovative and reliable products.
Automotive Industry
The automotive sector heavily relies on Industrial Plastic Molding to produce a wide array of components. Raw liquid plastic is transformed into essential parts through a precise manufacturing process. This includes everything from dashboards and interior fittings to exterior panels. The application of technical resins ensures durability and performance in diverse conditions. Companies often invest in custom moulds to achieve the specific shapes and sizes required for various automobile models.
Plastic drums and other molded components are not only lightweight but also resistant to corrosion. The efficiency of the first plastic injection allows for rapid production, helping to meet the demands of industrial projects in the automotive industry. By optimizing the use of liquid resin, manufacturers can create intricate designs and maintain high standards of quality. This versatility makes Industrial Plastic Molding indispensable in modern automotive production.
Consumer Goods Sector
Industrial Plastic Molding plays a significant role in the consumer goods sector by providing a variety of solutions for product manufacturing. The use of different resins allows for tailored properties that meet specific performance requirements. Companies often choose standard materials with additives to enhance durability and functionality. Mould walls are designed carefully to facilitate the production of intricate shapes and intricate designs. This versatility supports the creation of numerous extruded products that cater to consumer needs efficiently.
Quality and efficiency are crucial in the production of consumer goods. Industrial Plastic Molding enables manufacturers to replicate metal parts with remarkable precision, reducing the reliance on traditional metal fabrication processes. Excess material is minimized during production, promoting sustainability. Resin recommendations guide manufacturers in selecting the appropriate materials, ensuring that the final products meet desired standards while being cost-effective. As a result, the consumer goods industry benefits greatly from the advancements in Industrial Plastic Molding.
Medical Devices and Equipment
The use of Industrial Plastic Molding in the medical field ensures the production of reliable and durable end products crucial for patient care. Various tools and techniques allow for the incorporation of metal inserts to enhance structural integrity. This approach is particularly effective for creating even-walled products that maintain consistent performance under variable conditions. By utilizing advanced materials, manufacturers can produce equipment that withstands rigorous use while remaining cost-effective.
Durability is a key characteristic of medical devices that utilize Industrial Plastic Molding techniques. The process enables the creation of items that resist wear and tear, reducing the prevalence of broken metal parts and ensuring longer operational lifespans. Manufacturers prioritize material efficiency, leading to designs that maximize functionality without unnecessary waste. As the demand for cutting-edge medical equipment grows, the role of Industrial Plastic Molding will continue to expand, delivering innovations that enhance patient outcomes.
Advantages of Using Plastic Molding
Industrial Plastic Molding offers significant advantages that enhance manufacturing efficiency and product quality. This process allows for the creation of tight-tolerance precision plastic components, which are essential for applications requiring detailed specifications. The use of a full production tool enables manufacturers to produce items such as hollow containers and bulk containers with consistent quality and reliability. Techniques such as screw injection contribute to the versatility of forming various shapes and sizes, which is crucial in meeting diverse industry needs. The ability to utilize a wide range of materials in the molding process further supports innovation and customization in the production of plastic products.
Cost-Effectiveness
Industrial Plastic Molding offers significant cost advantages that make it an attractive choice for manufacturers. The full production injection process allows for the efficient creation of complex products while requiring little material waste. Utilizing steel type P20 for tooling enhances durability and performance, ensuring that molds can withstand the rigors of production over time. This efficiency translates into lower costs per unit, making it easier for businesses to meet their budgetary goals.
The process involves cooling, which is a crucial step in achieving optimal product quality and consistency. With medium tooling options available, companies can strike a balance between upfront investment and long-term savings. By producing a high volume of usable products quickly, Industrial Plastic Molding maximizes output while minimizing expenses. This combination of factors positions injection molding as a cost-effective solution in the competitive landscape of manufacturing.
Precision and Reproducibility
Industrial Plastic Molding is renowned for its ability to produce parts with exceptional precision. This capability is critical when manufacturing items like lids and containers, where a specific thickness is essential for functionality and aesthetics. For example, certain containers used for food storage must fit securely to ensure freshness, while refrigerator liners require precise dimensions to effectively fit into appliances. The accuracy of the molding process ensures that each piece meets high-quality standards.
Reproducibility is another significant advantage of Industrial Plastic Molding. Once a mold is created, it can consistently replicate complex designs across large production runs. This is particularly valuable in industries requiring a vast number of identical components, such as stainless steel parts or heated cylinder applications. The reliability of the molding process not only optimizes production efficiency but also minimizes waste and reduces costs, solidifying the role of plastic molding in various sectors.
Factors Influencing the Molding Process
The success of Industrial Plastic Molding heavily relies on several critical factors that directly influence the quality of the final product. Material selection plays a pivotal role, as using inexpensive materials can significantly reduce costs while still providing adequate performance. The machines heat and the heating process must be carefully calibrated to ensure optimal melting and flow of the plastic. For instance, a pre-hardened P20 tool may be necessary for creating precision-engineered parts, which are essential in industries that demand strict tolerances. In-house engineering expertise is vital for troubleshooting and optimizing these factors, ensuring that the production process is efficient and effective. Just as a jello mould shapes its contents, the molding process must be finely tuned to achieve the desired results.
Material Selection
Selecting the right materials is crucial in Industrial Plastic Molding, as it directly influences the efficiency of the production process. Different types of plastics offer varying properties, such as strength, flexibility, and resistance to environmental factors. These characteristics play a significant role in determining the suitability of a material for specific products. Automated technologies can enhance the selection process, ensuring that the most appropriate materials are chosen to deliver a high-quality final product.
The injection process in Industrial Plastic Molding requires careful consideration of the material's behavior under heat and pressure. Understanding how different plastics react during molding can impact the durability and functionality of the final product. Proper material selection not only affects the aesthetics but also influences the production costs and time. It is essential for manufacturers to weigh the pros and cons of each material to optimize their production capabilities.
Temperature and Pressure Settings
Temperature and pressure settings are critical factors in Industrial Plastic Molding processes. Each molding technique, such as compression molding and rotational molding, requires specific temperatures to ensure the molten plastic flows properly and fills the mold. For instance, in injection molded applications, maintaining the right temperature ensures that the plastic material reaches the desired viscosity, allowing for accurate shaping and detailing. Similarly, in extrusion moulding, precise temperature control is essential to produce consistent profiles, whether for plastic bottles or custom components.
The pressure applied during molding significantly impacts the quality of the final product. In processes like injection molding and compression molding, adequate pressure is needed to compact the molten plastic into the mold cavity effectively. This ensures minimal air pockets and defects, leading to superior manufacturing outcomes. Understanding the interplay between temperature and pressure allows manufacturers to optimize production cycles while ensuring that each molded part, whether it be a small component or large consumer goods, meets stringent quality standards in Industrial Plastic Molding.
Conclusion
Industrial Plastic Molding plays a crucial role in modern manufacturing, providing efficient and cost-effective methods for creating solid plastic parts. The use of molding dies and prototype molds allows manufacturers to produce a wide range of plastic replacement parts with precision. Innovations in plastic powder developments have expanded possibilities for utilizing various plastic resins in the molding process. Techniques such as roto-molding tools enhance production capabilities, ensuring the creation of high-quality components suited for diverse applications. The ongoing evolution of industrial plastic molding continues to shape industries by delivering reliable solutions and meeting the growing demand for durable plastic products.
FAQS
How are parts molds designed for plastic moulding and what processes are involved when the mold cools?
The design of parts molds for plastic moulding is crucial as it impacts how efficiently the material is used. The process involves cooling, which allows the plastic to solidify after being poured into the mold. Different types of molds, such as rotational molds or thermoform molds, are utilized depending on the specific requirements of the project. Once the mold cools and the product is formed, it builds the desired shape with precision.
What steps should be taken to make a thermoform mold ready for production while ensuring the process is material efficient and includes effective cooling?
To make a thermoform mold ready for production, first, select the right materials that enhance the material efficiency of the mold. The process involves cooling methods that are crucial in maintaining the shape and integrity of the final product. After molding, it’s essential to implement effective cooling techniques to ensure that the material sets properly and achieves the desired quality in production.
What techniques can be employed to enhance the cooling phase in a production mold while ensuring it remains material efficient?
To enhance the cooling phase in a production mold, techniques such as optimizing the mold design for uniform wall thickness and integrating cooling channels can be employed. These methods help achieve a material efficient process by reducing cycle times and energy consumption. Additionally, understanding the properties of the material involved can improve the cooling efficiency, ensuring that the entire process involves cooling effectively.
What are the key considerations in the production process that involve cooling for plastic molds?
In the production process of industrial plastic molding, the key considerations that involve cooling include the design of the mold, the choice of materials, and the cooling channel layout. Effective cooling is crucial as it impacts the cycle time and the overall quality of the molded parts. Properly managing the cooling phase ensures that the material sets correctly and helps prevent defects, thus enhancing the efficiency of the production process.
What are some best practices for ensuring effective cooling during the production process of plastic molds?
Effective cooling in the production process can significantly impact the quality of molded parts. To ensure proper cooling, it is essential to design molds with adequate coolant channels, utilize materials that enhance thermal conductivity, and continuously monitor the temperature throughout the process. Implementing these best practices in the production process can optimize production efficiency while also addressing aspects of the process that involve cooling.
What factors influence the overall production process when we consider how they involve cooling in plastic molding?
The production process can be significantly influenced by various factors that involve cooling, such as the design of the mold, the type of plastic used, and the cooling methods implemented. Effective cooling is crucial as it helps in reducing cycle times and preventing defects in the molded parts. Additionally, the thermal conductivity of the mold material and the placement of cooling channels also play vital roles in optimizing the cooling process in plastic molding.
What additional elements should be considered in the production process for plastic molds to ensure that they effectively involve cooling?
When discussing the production process for plastic molds, it is crucial to consider factors like mold design, heating and cooling channels, material type, and cycle times, as these elements all influence how effectively the process involves cooling.
What are some innovative methods that can be implemented to optimize the production process that involves cooling for plastic molds?
To optimize the production process that involves cooling, manufacturers can utilize innovative methods such as implementing advanced cooling channel designs and using materials with enhanced thermal conductivity. Additionally, incorporating simulations to model heat distribution can improve the cooling efficiency. These strategies help ensure that the cooling process is effective and reduces cycle times in plastic molding.
What is the role of temperature management in the production process and how does it involve cooling for plastic molds?
Temperature management plays a crucial role in the production process of plastic molds, as it directly influences the quality and efficiency of the final products. Effective temperature regulation helps maintain the right conditions during the molding process, ensuring that cooling is uniform and controlled. This not only enhances the mold's performance but also reduces the risk of defects, making the production process involve cooling more effective and efficient.