Lubrication Engineer's Provides Lubricants For The Cement Industry
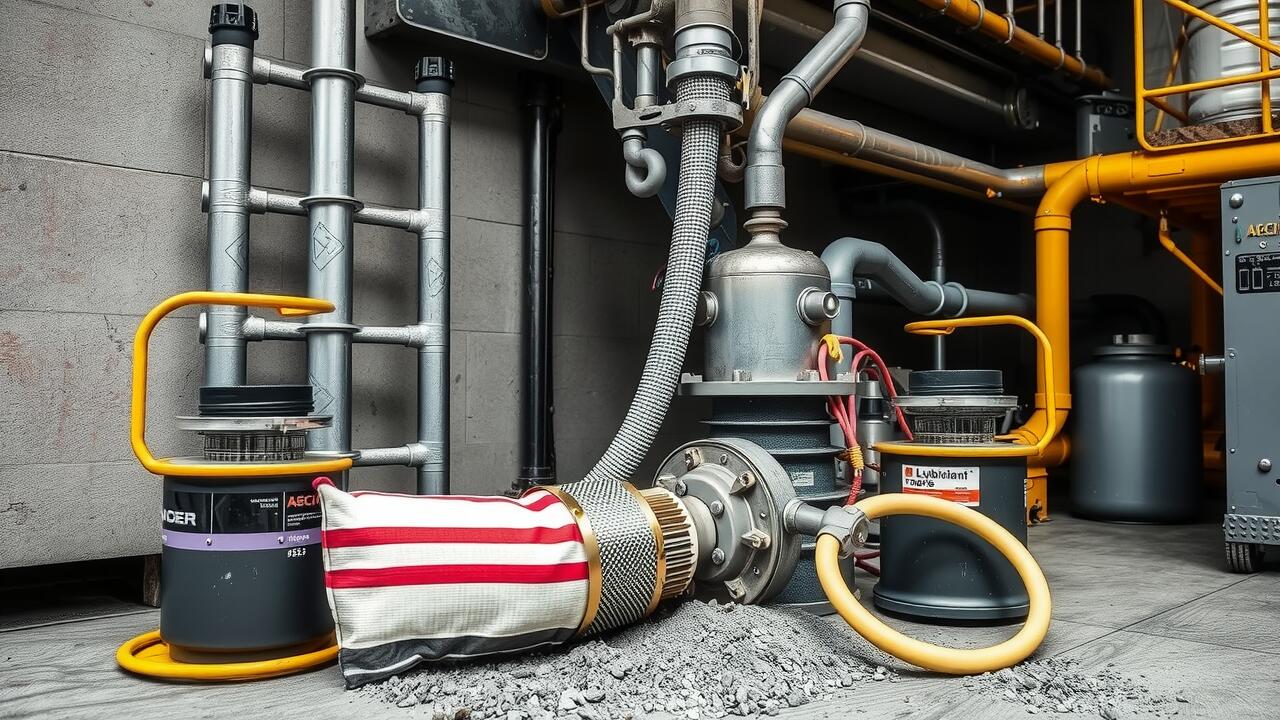
Lubricant Application Techniques in Cement Plants
Effective application of lubricants is crucial in the demanding environment of cement plants. Techniques such as centralized lubrication systems ensure that machinery receives the correct amount of lubricant at the right intervals, minimizing wear and optimizing equipment lifespan. Automated systems can significantly reduce human error, ensuring a consistent supply of lubricant to key components like bearings and gears.
Another innovative approach involves the use of precision lubrication, which applies lubricant only where needed. This method not only improves efficiency but also reduces waste. Utilizing spray lubrication or brush systems allows for targeted application, helping to maintain cleanliness and efficiency in operations. Both techniques ultimately contribute to enhanced performance and reliability of cement plant machinery.
Best Practices for Effective Lubrication
Effective lubrication is essential for maintaining the performance and longevity of equipment in cement plants. Regularly scheduled lubrication intervals should be established based on manufacturer recommendations and operational conditions. This involves assessing factors such as temperature, load, and environmental conditions to determine the appropriate lubrication frequency. Utilizing the correct type of lubricant, whether synthetic or mineral-based, is also crucial. Selection should account for the specific requirements of the machinery, including viscosity and compatibility with seals and materials.
Another key aspect involves ensuring proper application methods. Employing techniques such as centralized lubrication systems can enhance efficiency and accuracy, minimizing waste and exposure to contaminants. Staff training is equally important to ensure that personnel understand the importance of lubrication and can identify potential issues before they lead to equipment failure. Conducting routine inspections and adhering to best practices can significantly contribute to the overall reliability of cement plant operations.
Innovations in Lubrication Technology
The field of lubrication technology has seen remarkable advancements aimed at enhancing the efficiency of equipment in cement plants. New formulations of lubricants are being developed to improve performance under extreme conditions, such as high temperatures and heavy loads. These innovations often incorporate synthetic base oils, which provide superior stability and reduce the frequency of oil changes. Additionally, additives designed to combat wear and tear are becoming more sophisticated, offering protection that improves the lifespan of machinery components.
Recent advancements also include the integration of smart lubrication systems that utilize IoT technology. These systems enable real-time monitoring of lubricant conditions, ensuring optimal performance at all times. By analyzing data from sensors, operators can predict when maintenance is required, significantly reducing downtime and improving operational efficiency. Such innovations not only enhance productivity but also align with the industry's move toward automation and smart manufacturing processes.
Advancements Benefiting the Cement Industry
Recent advancements in lubrication technology have significantly impacted the cement industry, enhancing machinery performance and reliability. Synthetic lubricants, designed to withstand extreme temperatures and pressures, provide superior protection against wear and tear. These high-performance oils can extend the service life of equipment, reducing the frequency of maintenance and replacements. Additionally, the development of specialized greases featuring advanced additives ensures optimal lubrication even in the challenging environments found in cement plants.
Another notable innovation is the implementation of automatic lubrication systems, which ensure consistent application of lubricants across various machinery components. These systems minimize human error and reduce the risk of over-application, which can lead to contamination and inefficiency. By automating lubrication processes, cement plants can achieve improved operational efficiency and reduce downtime. The integration of smart technology, such as sensors that monitor lubricant levels and conditions, further enhances the ability to maintain optimal performance in equipment.
Environmental Considerations in Lubricant Usage
Sustainability has become a critical focus in the cement industry, prompting companies to reevaluate their lubrication choices. The environmental impact of lubricants, including their biodegradability and toxicity, is essential when making decisions about lubricant usage. Selecting eco-friendly products minimizes harmful emissions and reduces contamination risks, aligning operations with environmental regulations and corporate sustainability goals. By opting for bio-based or synthetic lubricants, companies can significantly lessen their ecological footprint while maintaining equipment performance.
Implementing sustainable practices demands diligence in lubricant application and disposal methods. Regular assessments of lubricant performance can spotlight opportunities to optimize usage and reduce waste. Proper disposal methods for used lubricants are crucial to prevent soil and water contamination. Collaborating with lubricant manufacturers to develop more sustainable products can also facilitate smoother operations and contribute to a greener cement production process. Such initiatives promote not only environmental stewardship but also cost savings in the long term.
Sustainable Practices in Lubrication
The shift toward environmentally friendly operations in cement plants has led to a reevaluation of lubricant usage. One effective approach is the adoption of bio-based lubricants. These options typically come from renewable resources, reducing dependence on fossil fuels and lowering greenhouse gas emissions associated with traditional petroleum-based products. Additionally, the implementation of proper storage practices minimizes the risk of contamination and spills, further enhancing the overall sustainability of lubricant application.
Monitoring the performance and condition of lubricants can also contribute to sustainable practices. Utilizing advanced technologies such as condition monitoring systems allows for real-time assessment, optimizing lubricant life and reducing waste. By tracking lubricant degradation, maintenance teams can schedule replacements and cuts downtime, which minimizes the environmental impact of lubricant disposal. These proactive measures can significantly improve resource efficiency within cement plants while promoting a more sustainable operational model.
Monitoring and Analyzing Lubricant Performance
Effective maintenance of machinery in cement plants relies heavily on the consistent monitoring and analyzing of lubricant performance. Employing advanced techniques such as oil analysis can provide critical insights into lubricant condition and machine health. Regular sampling and testing can identify contaminants, viscosity changes, and degradation, allowing for timely interventions that prevent equipment failures. This proactive approach ultimately extends the life of machinery while optimizing operational efficiency.
Data-driven analysis plays a crucial role in making informed decisions regarding lubricant usage. Implementing condition-based monitoring systems enables real-time tracking of lubricant performance metrics. This technology helps in identifying patterns that signal potential issues, enabling maintenance teams to adjust their strategies accordingly. By leveraging these insights, cement plants can streamline their lubrication processes, ensuring that each component operates within its optimal parameters.
Techniques for Maintenance Optimization
Optimizing maintenance involves a range of techniques that ensure machinery runs efficiently while minimizing downtime. One effective approach is implementing predictive maintenance, which utilizes data analysis to forecast equipment failures before they occur. By monitoring parameters such as vibration, temperature, and lubricant condition, technicians can identify potential issues early, allowing for timely interventions. This strategy not only prolongs the life of machinery but also reduces unexpected breakdowns, leading to smoother operations.
Regular oil analysis is another vital method for enhancing maintenance processes. By examining lubricant samples for contaminants and degradation, maintenance teams can gauge the health of both the lubricant and the machinery it services. This information helps in adjusting maintenance schedules based on actual equipment conditions rather than fixed intervals. By integrating these techniques into the maintenance routine, cement plants can achieve higher reliability while optimizing both their resources and operational costs.
- Invest in training for maintenance staff to empower them with knowledge of new technologies and techniques.
- Utilize condition-based monitoring tools to track equipment health in real-time.
- Implement a computerized maintenance management system (CMMS) to streamline scheduling and documentation.
- Develop a preventive maintenance schedule to regularly assess and address equipment needs before issues arise.
- Encourage collaboration across teams to share insights and improve maintenance strategies collectively.
- Conduct regular audits of maintenance practices to identify areas for improvement.
- Leverage analytics and reporting to measure maintenance effectiveness and inform future decisions.
FAQS
What are the main lubricant application techniques used in cement plants?
The main lubricant application techniques in cement plants include centralized lubrication systems, manual lubrication, and automatic lubrication systems. Each method is selected based on the specific machinery requirements and operational conditions to ensure optimal performance.
What are some best practices for effective lubrication in the cement industry?
Best practices for effective lubrication include selecting the right lubricant for each application, regular maintenance schedules, monitoring lubricant levels, and ensuring proper application techniques to minimize waste and maximize efficiency.
How has lubrication technology advanced in recent years for the cement industry?
Recent advancements in lubrication technology include the development of high-performance synthetic lubricants, smart lubrication systems that use IoT for real-time monitoring, and improved formulations that enhance equipment longevity and reduce environmental impact.
What environmental considerations should be made when using lubricants in cement plants?
Environmental considerations include selecting biodegradable lubricants, minimizing spills and leaks, implementing proper disposal methods for used lubricants, and adopting practices that reduce the carbon footprint of lubrication operations.
How can monitoring and analyzing lubricant performance benefit the cement industry?
Monitoring and analyzing lubricant performance can help in identifying potential equipment failures, optimizing maintenance schedules, reducing downtime, and ultimately enhancing the overall efficiency and longevity of machinery in cement plants.